|
|
ここでは粉末造形のちょっと難しいところをオペレーターの目線から紹介したいと思います。 |
まずは樹脂の収縮です。樹脂は熱を加えると膨張し冷ますと縮む性質があるのですが、高温で造形をするこのマシンにおいてはこれを読むのがとても重要になります。
冷めて取り出す際にベストな状態になるようにあらかじめモデルを拡大するわけですが、これがとても微妙なもので困り者です。
材質、形状などによって少しずつ変えていきますが大きなウェイトを占めるのはやはりデータ取りになってきます。 |
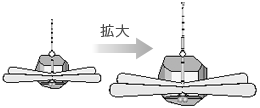 |
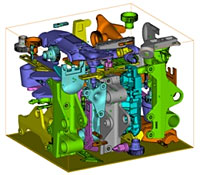 |
続いて配置。粉末造型機は金属フレーム(水槽のようなもの)の中に上手に様々な仕事を詰め込んでいく配置という作業がうまくできると効率の良い仕事になります。
ただ何でもかんでも詰め込めば良いと言うものでもなく、良い造形ができる傾きや位置、また納期に間に合う高さ…など考慮に入れた上で固めていくわけです。
当然、たくさん集まってからパズルのように組んでいくのが良いのですが、短納期の時代です、集まってくるのを待って造形と言う訳にはなかなかいかないのが現実ですが…。 |
最後は材料の混合比率です。未焼結パウダ(造形物以外の固まらなかった材料)は繰り返し使うことができるのですが、このリサイクル材だけでは美しい造形はできません。
ここで新しい材料と混ぜなければなりません。この混合比を見誤ると肌荒れのような現象(オレンジスキン)が浮き出てくるのです。NEW材を増やせば安定しますがコストが上がり、過剰に減らせば安定しません。この間をうまく取るのがとても難しいのです。
また何回繰り返して使うかも大きなポイントの一つになります。とにかく材料をうまく賢く使うことも造形にとっては大事なことなのです。 |
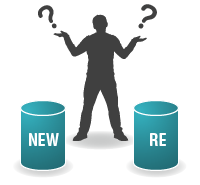 |
このように造形は様々な条件が揃って初めて納得できるものとなる訳です。
いまだにうまくいかないですけどね。 |
|
|