 |
|
º£²ó½ÐÉʤ·¤¿¡Øball in cube¡Ù¤¬¡Ø»îºî¡¦¥Æ¥¹¥È²Ã¹©ÉôÉÊÉôÌç¡Ù¤Ë¤ª¤¤¤ÆÆ¼¾Þ¤ò¼õ¾Þ¤·¤Þ¤·¤¿¡£²áµî2²ó¡¢Æ±¥³¥ó¥Æ¥¹¥È¤Ë½ÐÉʤ·¤Æ¤ª¤ê¤Þ¤¹¤¬½é¤Î¼õ¾Þ¤È¤Ê¤ê¤Þ¤·¤¿¡£
¼ø¾Þ¼°¤Ï2009ǯ11·î12Æü¤Ë(³ô)¿¹Àºµ¡À½ºî½ê(¸½DMG¿¹Àºµ¡(³ô)) °Ë²ì»ö¶È½ê¤Ç¹Ô¤ï¤ì¤Þ¤·¤¿¡£½ÐÉʤ·¤¿¼õ¾ÞºîÉÊ¤ÏÆ±»ö¶È½ê¥·¥ç¡¼¥ë¡¼¥àÆâ¤ËŸ¼¨¤µ¤ì¤Æ¤¤¤Þ¤¹¡£
|
¢¨ |
º¸¤«¤é4¿ÍÌܤ¬¼õ¾ÞºîÉʤκîÀ½¤òôÅö¤·¤¿
»îºîÉô »îºî1²Ý ±º¥ê¡¼¥À¡¼ |
|
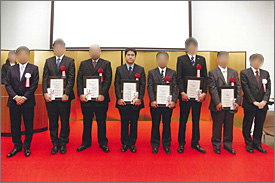 |
|
Âè6²ó ÀÚºï²Ã¹©¥É¥ê¡¼¥à¥³¥ó¥Æ¥¹¥È
»îºî¡¦¥Æ¥¹¥È²Ã¹©ÉôÉÊÉôÌç 2009ǯ11·î12Æü
(³ô)¿¹Àºµ¡À½ºî½ê(¸½DMG¿¹Àºµ¡(³ô)) |
|