|
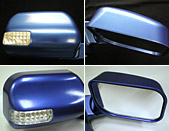 |
|
Click the picture to enlarge |
|
|
This is the modeling product (prototype) that is processed by 3D-CAD (NX).
The body of the side mirror is produced by the SLS (Selective Laser Sintering) Rapid prototyping machine, and then it is painted after the surface treatment. The part of winker is made of acrylic material that is processed by cutting like a diamond shape using the technique of "mirrored acrylic cutting & grinding process". In addition, the mirror part is movable using some mechanical parts. In this way, by performing second processing, the possibility and the applied range of a modeling product (prototype) can be widely expanded. |
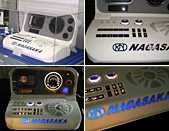 |
|
Click the picture to enlarge |
|
|
We used the maximum work size of SLS (Selective Laser Sintering) machine, W700×D380×H580mm, to generate this one-piece prototype. The meter panel and handle knob in front were finished by mirrored acrylic cutting & grinding process. The name plate of Nagasaka was secondarily processed by acrylic cutting & grinding technique and mounted because it is difficult to accomplish 1/100mm accuracy by only using SLS method. This is one of the sample cases that realized our unique prototyping technology using both of Rapid Prototyping System and Cutting & Grinding technique. |
|